Our Product
The product we have designed is a windshield treatment that reduces glare from natural
and artificial lights through the use of a moth-eye diffraction grating.
"In some respects, they (moth-eye gratings) behave similarly to photonic
crystals, but have the advantage that their behavior is somewhat easier
to predict. Designing them for the scale of a windshield would be quite a
challenge, but probably possible."1 Like all diffraction
gratings, its purpose is to alter the behavior of light. In our case we
are doing it on the nano-scale so that the treatment is invisible to
the naked eye. If this application were to be prohibitively expensive,
the use of eye sensors could strategically position a minimal amount of material in a specific location.
It is noteworthy that "many vehicles in Florida have OEM (Original
Equipment Manufacture) used reflective glass coatings that
appear reflective with a violet color to the naked eye. Some GM minivans
and the Buick Rendezvous from 1990-2003 have such coatings as to current
luxury vehicles like high end Audi's, BMW's, and Mercedes."2
In an email dated February 16, 2007, Dr. Dobson conjectured that "it is
easier to design moth-eye structures which work at a specific wavelengths ... I
don't think that there is any reason that such a structure could not be designed
to have very good antireflective properties over a wide range of wavelengths."3
In another email dated February 27, 2007, Dr Dobson conjectured that "If
you applied several layers of such a grating structure (several sheets
of very thin film, each with a different grating pattern), the resulting
composite could look a lot like a photonic crystal...by applying several
layers you should be able to get both good antireflectivity and good
polarizing filters."4
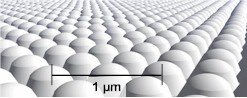
Image courtesy of Sean B.
Looking at the next diagram one sees the headlight of an oncoming car reaching a
windshield treated with a moth-eye grating on the inside of the
windshield. The intensity of the headlamp's beam
is diffused so that the driver would no longer be blinded by the beam.
In essence, we are dispersing the intensity over a larger area to reduce the level
of intensity that strikes the eye.
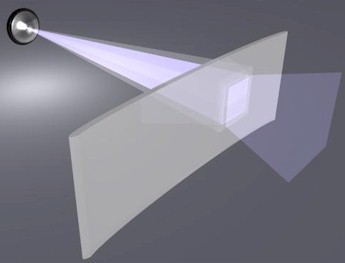
Image courtesy of Sean B.
In this second series of pictures one sees how a treated windshield would allow
the driver to see road hazards that he would otherwise be unable to distinguish
if his eyes had to adjust to the glare from oncoming headlights.
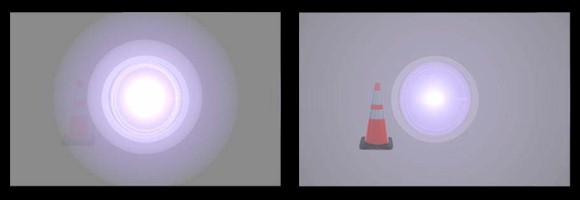
Image courtesy of Sean B.
The embossing of such a grating would be minimally invasive to the existing manufacturing
process.
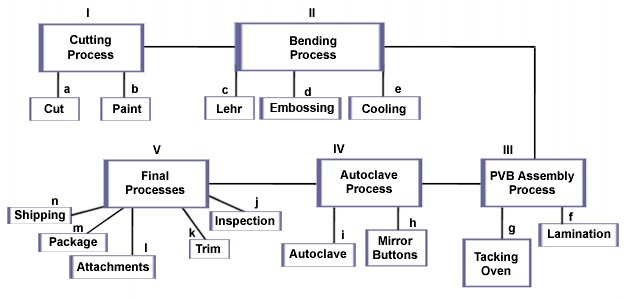
Image courtesy of Sean B. and Forrest R.
I - Cutting Process: Float glass is brought into the plant
from a separate facility. Float glass is a large block of raw
glass, that is passed along a bed of molten tin. The molten tin is
dense enough to float a block of glass, thereby earning its name
"float glass". The raw glass pattern
is cut out, separated from the raw glass, then has the edges smoothed. After the
edges are smoothed, two pieces of glass are washed and paired together.
- Cut: The cut
area is when the glass is cut into panels that are the right size for windshields.
The float glass is cut into several small panels, then further defined to the dimensions
of the windshield. The excess scrap is then placed out of the way.
- Paint: The
newly cut windshields have a black paint applied to the
edges of the glass pane to keep them together and to shied
the urethane glue, which holds the windshield in the car,
from UV rays.
II - Bending Process: The bending process
is where the shape of the windshield actually takes form. Many windshields can be
pressed at one time, making this a very efficient process.
- Lehr: The glass pieces are sent into
the furnace, or lehr, for bending. The windshields pass around the furnace like
a carousel. On the carousel the glass is melted to a plastic state. This glass is
then bent by its own weight. The glass is finalized by having the glass pressed
inside a mold to get the correct dimensions.
-
Embossing Masters:
This is where our moth-eye grating would be applied. The windshields would
be sent across the assembly line to a robot. The glass is then aligned
and the embossing master starts. We would apply it to the back of the
windshield. After the application of the moth eye grating, the windshield would
move further down the assembly line to the finishing department.
- Cooling: The cooling process is where
they turn the lehr's power off to let the
windshields cool. They must be allowed to cool at a slow rate in a
controlled environment to properly anneal the windshield, minimizing
the uniform stresses.
III - PVB Assembly Process: The PVB process
is very important. PVB makes the window legal, by keeping the windshield together
in case it shatters. The PVB also holds the two pieces of glass together, making
them one solid piece.
- Lamination:
This is were PVB is added to the inside of the windshield. The two windshield pieces
are lined up with a PVB sheet in the middle. The three pieces are then combined
and molded together to form one piece. The Windshield is then passed onto the tacking
oven.
- Tacking Oven:
In the tacking oven the excess PVB and the black paint is trimmed from the edge
of the windshield. However, the PVB in its current state is semi-cloudy.
It must be sent to the autoclave.
IV - Autoclave Process: The autoclave process
is the clarifying process. Without this step, your windshields would be dark, cloudy,
and unable to see through.
-
Mirror Buttons: The mirror buttons are added on the inside
of the windshield while in the autoclave.
-
Autoclave:
The autoclave is a heating oven that is several hundred degrees. The temperature
is not hot enough to melt the glass, but is high enough to clarify the PVB inside
of it. After one and a half hours, the batch of windshields are removed from the tacking
oven. These semi-finished windshields are totally transparent and resemble the final
product.
V - Finishing: The finishing process is
where all the accessories are added, including electrical wires and adhesive attachments.
-
Inspection: Windshields are inspected and checked over to make sure all defects
and abnormalities are removed from the product.
-
Trim: This
is where excess PVB is again trimmed from the glass that seeped out from the autoclave
process.
-
Attachments:
This stage is were GPS systems, rain sensors, or electrical wires are attached to
the windshield.
-
Packaging:
The packaging process is where the glass is stacked, boxed, and placed on trucks
to be dispersed.
-
Shipping: The
shipping is the last and final process before going to the client that ordered the
windshields. They go by trucks to warehouses were they are sorted by destination,
reloaded to the individual routes, and sent on to the receivers.
After the glass is cleaned from the autoclave, it proceeds to a robot which
has the tools necessary for the embossing master. Because windshields are
made in large quantities (usually 500,000 or more at a time), the robot could use
a code for the geometry of each windshield configuration. These "codes"
could be made by using 3D-modeling, or parametric-modeling, software such as Autodesk
Inventor.
The embossing process is like a large stamp. A pre-made grating is heated
to large temperatures. This stamp comes down upon the windshield, and quickly
stamps the moth eye design into the glass. This quickness allows it to
be created at a rate of one per second, barely affecting the length of the assembly,
especially if multiple Embossing Masters are used. The Stamp itself
hardly ever
wears, and very seldom has to be replaced, making it extremely low maintenance.
As a new windshield approaches the robot, the code could be changed. For instance,
you could enter the product number for that windshield, and the robot would re-align
itself for the new geometry dimensions for that windshield. This can be done repeatedly
and efficiently using codes for each windshield's geometry. This automated, mechanized
process would help to eliminate human error and reduce the creation of scrap windshields
that cannot be used and would have to be discarded.
Or perhaps, the robot could be outfitted with dimension readings
so that it can automatically detect when a new "style of
windshield" comes through the assembly line. It could re-align
the new windshield and use pre-set geometry settings
to start a new embossing master. The robot could detect for
itself the changes needed for each windshield configuration.
Since the embossing master would be on the outside surface of the windshield, it
would not interfere with the PVB laminate in the middle of the windscreen. Our nanoscale-grating
would be undetectable to the naked eye and would not interfere with the windshield's
everyday functionality.
|