PVB and Windshield Manufacturing
The following manufacturing process is closer to that of the aftermarket,
windshield replacement process. The windshields used in the production of entire
automobiles are made on a much lager
scale for mass volume and high speed production.
Windshield manufacturing is done in an assembly line manner which contains two
components: Float Glass and Polyvinyl Butyral (PVB) Interlayer. The
manufacturing company buys these components from a supplier and combines
them to make a windshield in a process called laminating.
The float glass layers from the factory are curved together as matching pairs by separately
heating them to 620 degrees Celsius. The temperature is varied widely so as to form complex shapes, required by today's varying windshield design, through press-bending or regular gravity sagging. The shaped glass pairs are then cooled to room temperature before the PVB laminate can be sandwiched between them. This lamination process is actually
forming a safety glazing that keeps the glass in place in case of breakage and affords the driver some degree of visibility
in emergency situations.
The PVB is bought in large rolls and goes to a multistage process before being combined with the float glass and
placed into the furnace. PVB is refrigerated in storage or interleaved because at room temperature the polymer
becomes soft and tacky, making it stick
together.1 A processing line is used to manipulate the PVB into the desired shape, thickness
and curvature, to cut it, and to stack it with the sheets of float glass.
If the PVB has a sunshade band along the top edge then the PVB is sent through a manipulation process to shape the PVB. A machine begins the shaping and curving process by using a moderate amount of heat to
first soften and thin the PVB sheet so that it can attain a curve when it is
later rolled over a conical roller while under tension to stretch one side of the film.
This is done so that the sunshade band has a proper curvature to match the
roofline of the car that will receive the windshield.
The second step is to run the PVB through a relaxation unit. This step requires at least
half an hour for the PVB to settle into its final shape and curvature.
The final step in this process is the cutting of the PVB into individual sheets. This machine can cut the PVB at an angle from 0 to 25 degrees to accommodate the different shapes of car models.
This process is done to reduce the amount of waste involved with cutting excess PVB from a rectangular sheet.
After the glass is bent it is put inside a vacuum bag. When under the vacuum condition the pressure
holds the PVB in place between the layers of glass to remove air bubbles. The vacuum bags are then put into an oven called an
autoclave which heats the vacuumed windshield. The entire setup reaches 135°C to 145°C,
thereby melting the PVB, making it transparent, and fusing the three layers into one. The quality of lamination, or adhesiveness between the PVB and
the layers of float glass, are dependent on the temperature within the autoclave and the effectiveness
of the pressure on the layers of glass and PVB. A combination of vacuum packing and pressurized heated air inside the autoclave must be 175 psi
for the PVB to adhere to both layers of glass. Before going into the autoclave the PVB
appears opaque due to a pattern embossed on the surface that severely diffracts
light.2 The
autoclave uses heat and pressure to press out the embossed pattern and dissolve
any trapped air. If the temperature is too low, the PVB will not melt entirely
and will remain cloudy. If it is too hot the PVB will discolor.
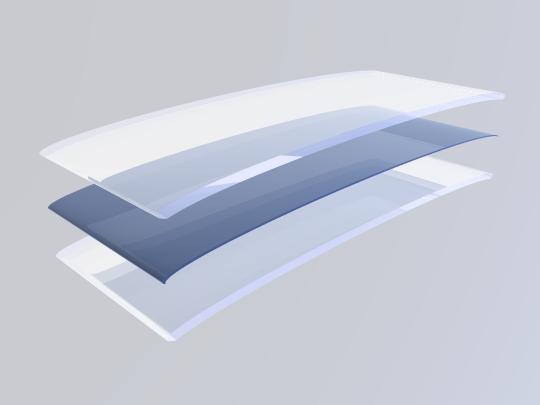
Image courtesy of Sean B.
|