Piezoelectricity is the conversion of electrical pulses to mechanical vibrations,
and vise-versa, the conversion mechanical vibrations back into electrical energy.
Adding
a force to the material (like squeezing it), will create an electrical current,
while pulling it apart, or releasing the stress, creates a current in the opposite
direction. The fact that these materials can produce currents in two different directions
is a characteristic unique to piezoelectrics.
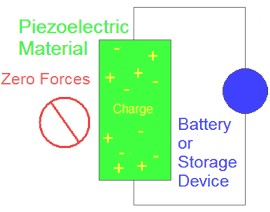 |
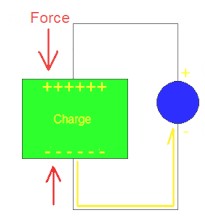 |
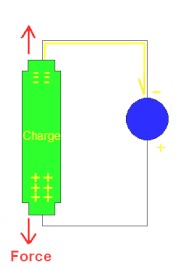 |
Images courtesy of Forrest R. |
The first picture represents a piezoelectric material 'at rest'. The structures
of piezoelectric materials are electrically stable when not under pressure. Therefore
the electrons are free flowing throughout the material, giving the piezoelectric
effect a neutral charge. When a force is applied to the piezoelectric material and
it is compressed, in this case
PZT (Lead zirconate titanate), the electrons align to the polar surfaces
of the material depending on the objects original orientation. This charge on the
surface of the material can then be transferred, via circuitry, through a conductor
to a storage device, such as a
capacitor, that can in turn discharge the stored energy to a device requesting
the electrical potential for its purpose.
PZT - Lead zirconate titanate
PZT is a man-made piezoelectric ceramic material made of Lead,
P,
zirconium,
Z, and Titanium,
T. The special function that allows PZT
to be more conductive than any of the other ceramics in the same field is that when
placed under tension or compression, the
titanium atom shifts within the cubical structure of the lead zirconium,
creating an extensively strong pole and provides a better flow of electrons to surface
wires.
This better flow makes it a more efficient conductive material. This ceramic gives
a larger power output than other forms of piezoelectric transducers (i.e.
ratio of plastic piezoelectrics is (PVDF) produce 1.3 mW and PZT produces
8.4).
Piezoelectric Power Harvesting
The concept of harvesting power from piezoelectric materials is a relatively new
idea. Although harvesting power from footsteps has been researched, it has not been
implemented due to a low power supply.
DARPA's Heel-Strike Generator for Soldiers used foot strike technology to
produce close to 1-2 watts of power per foot strike. MIT's project of
Crowd Farming
produced enough power to keep two 60-watt light bulbs lit for one second.
Microstrain
Technologies developed a system to harvest energy from buildings using piezoelectric
cables. The Responsive Environments Group working at the MIT lab invented the
Magic Carpet in which electricity is created through piezoelectric wires
spaced 4" apart in a grid system on the floor of a room to power appliances.
Our particular device will be composed of the full area of a foot strike instead
of the amount of 4" wires the foot strike impacts. The Magic Carpet could build
up a charge of
9.5 volts over the course of 20-80 seconds in a capacitor to power our sensor
array as well as the display screen. The total area of the Magic Carpet piezoelectrics
impacted came out to be 17 cm
2. However, because our project
deals with the impact across the entire area of a foot, our power output will be
much greater. To calculate the area we would impact, we need the dimensions of a
size
10-1/2 shoe which has dimensions: 27.5 cm length by 10.4 cm wide.
Area = (base) (height)
Area = (10.4 cm) (27.5 cm)
Area = 286.4 cm2
If we take into consideration that work boots are generally larger than running
shoes, our average area comes out close to 287 cm
2. The
ratio of our device to the responsive Environments Group's Magic Carpet is as follows:
287 cm2 / 17 cm22 = 16.9
Therefore our shoes would builds up a charge that is almost 17 times stronger than
their charge, at a rate 17 times as fast to reach a charge of 9.5 volts. The Magic
Carpet was constructed of
Polyvinylidene Fluoride (PVDF). PVDF produces
1.3 mW and PZT produces 8.7 mW with the same amount of applied force.
Our shoe is made of PZT, which is stronger. Therefore, not only the ratio of area
for power difference, but the difference in material must also be considered. The
ratio of our material (PZT) to their material (PVDF) is:
8.4 mW / 1.3 mW = 6.46
If you take the difference in ratio of power production (about 6.5 : 1) in the material
and combine it with the ratio of the area we're covering (about 17 : 1) you get:
(6.5) (17) = 110.5
As our first responder moves our foot strike produces 110.5 times as much power
per foot strike as the Magic Carpet, and provides that power 17 times as fast.
To receive the most power from our piezoelectric setups, we are using a circuit
with two different
volt sensing switches. Because our piezoelectric shoes would produce a current
in two directions, they require
rectifiers to change their direction so that they do not draw current from
the circuit while expanding.
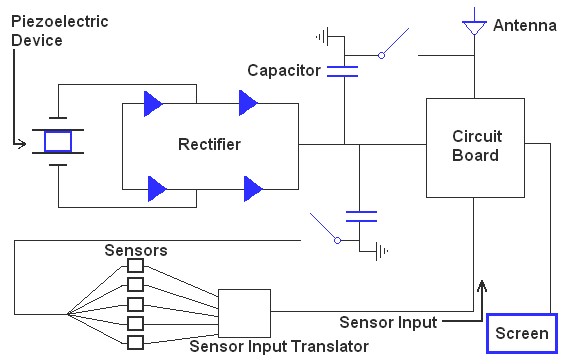
Image courtesy of Forrest R.
The subsequent DC current then passes to the
two capacitors and the
circuit board. Capacitors leading to the antenna and the sensors are different.
The one leading to the antenna takes 20 seconds to build up the power to relay to
the signal from the sensors to the
Helikite,
while the capacitor leading to the sensors discharge every 5 seconds to allow communication
to the circuit board through the
sensory translator (see Slide 24).
To eliminate the problem of the current traveling directly through the capacitor
because we are receiving a frequency, there needs to be volt sensing switches on
either sides of the capacitor. These switches are respectively the same as the capacitors
in response to discharging at the correct times, and close the circuit to keep the
capacitor charged and stops it discharging prematurely. Once the correct charge
is released, the capacitor sends the current to the switch, which closes to complete
the circuit to the device(s). The advantage of using volt sensing switches is that
power is not always required, and allows us to use power in bursts. The power not
consumed by the capacitors travels to the circuit board, which takes messages received
from the Helikite and transmits them to the
screen, which is receiving its power through the circuit board. The circuit
board also contains a small rechargeable device that keeps the power to the screen
on, and has the ability to draw from the charge on the capacitors in the event the
first responder stops creating a force on the shoes.
The demand of our system would be out of the range of feasibility without several
specifications unique to our design. This allows us to make the most use out of
the little power we can generate. Because there wouldn't be a significant difference
for the headquarters to make a decision based on information within 20 seconds,
we are saving 20 times the power by not sending it every second. We are also only
updating sensory information to the screen every 5 seconds due to the fact that
it also would not make a significant difference for the first responder to see conditions
in real time information, saving us 5 times the power by not sending every second.
The screen also contains a brightness feature that allows the first responder to
turn the screen brightness down whenever lighting from natural sources are enough
to make features of the screen visible. The settings of 5 and 20 seconds were chosen
so that they overlap whenever 20 seconds occurs, and is enough of a time interval
to display accurate information without being real time. To keep the capacitors
and battery charged for every 20 second message sending, the wearer should walk
at least 9 footsteps every 20 seconds, with the average person waling at a pace
of 25-30 steps at a casual walk. The small rechargeable battery located on the circuit
board allows for the signals to be received via the antenna, and helps power the
screen in situations when power supplied to the system reaches a low point. The
battery should be charged several seconds before the screen actually starts functioning,
which is about fifteen footsteps.
Zhong Lin Wang, a scientist at Georgia Tech, has created a fabric that can generate electricity,
by rubbing together microfibers that are coated with zinc oxide and gold. The direction
the fibers go, depends on the coating they receive.
These microfiber generators are made of crystals that are grown into the fabric
by immersing it in a zinc oxide solution for a period of time. Zinc-oxide nanowires
have been "grown" onto strands of
Kevlar nanofibers, and then a polymer is added to the tips helping the nanofibers
to remain attached to the fabric. Covering some of the fibers in gold and pairing
them with a zinc oxide fiber completes the assembly process for microfiber generators.
In the diagram below, the top fibers are coated in gold, and the bottom fibers in
zinc oxide.
These gold fibers serve as a
Schottky barrier, which means they make the energy generated go in one direction,
thus helping to store it. They can then rub together to produce electricity from
mechanical energy using what is known as the
piezoelectric effect. This piezoelectric effect is performed by certain non-conducting
materials when mechanical stress placed on them is converted into electrical energy.
These microfiber generators can put out
80 milliwatts per square meter of fabric (enough for a cell phone or ipod).
In the next picture, Zhong Lin Wang is holding up two microfiber generators in a
slide. The second picture is zoomed in on the tips of the microfiber generators.
The microfiber generator is actually an expansion of Zhong Lin Wang's previous invention,
the nanowire nanogenerator. This nanowire nanogenerator was made out of rougher
materials. Instead of gold fibers as the electrode, a different material containing
platinum tips was used. One problem still existed, the microfiber generator was
not waterproof.
Zhong Lin Wang recently invented a new generator known as the
flexible charge pump, which generates electricity by being stretched. Like
the previous generator, this flexible charge pump is made up of zinc oxide wires
and a shottky barrier to control the energy flow. This new flexible charge pump,
however, is encased in a polyimide which makes the pump waterproof and more durable.
A physical vapor decomposition method at 600 celcius creates zinc oxide wires. These
wires are then tipped with a paste serving as the electrode, and encased in a polyimide.
A
polyimide is a group
of extremely strong and durable (heat, chemical, radiation resistant, etc.) polymers
often used for tough jobs in items such as microwaves or vehicles.When the pump
is stretched the zinc oxide wires produce an electrical charge, due to the piezoelectric
effect, which runs in and out of the pump thus producing energy. The pump puts out
about 45 millivolts and is not on a nanometer scale (3-5 microns diameter, 200-300
microns in length). In the picture below, Zhong Lin Wang is shown holding up flexible
charge pump. The second picture is zoomed in on the flexible charge pump.
It can be made larger due to
better efficiency and easier construction. The pump could be connected, layered,
and put in clothing or even in the body. If put in the body, the pump could power
multiple sensors used to do things such as monitoring blood pressure. The next pictures
illustrate how a flexible charge pump would be constructed and a micrograph of an
actual pump.
Zhong Lin Wang has received funds towards his research totaling
$18 million US dollars
over the past 13 years. The companies that funded him were National Science Foundation,
Department of Energy, Defense Advanced Research Projects Agency, National Aeronautics
and Space Administration, National Institute of Health, China NSF, and industry.