Component Two - Product
Our liquid-cooled engine will be "constructed of almost entirely die-cast aluminum
(crankcase, cylinder, piston) - with some some components such as crankshaft and
connecting rod from forged steel."
(RH) The purpose of our design is
to improve combustion and thereby reduce pollution as in order to address the
upcoming 2006 marine emission
standards. Our technical application is pollution avoidance. Our product
integrates the following three hamonized technologies. TANAKA's crankcase and
delivery system, mechanical logic gates, and a dynamic mechanical switch.
- TANAKA crankcase and delivery system
The PureFire engine is an engine being Manufactured by TANAKA© Power Equipment Inc. that uses centrifugal force to
allow for more efficient fuel burning. It creates this centrifugal force through the use
of curved surfaces and high velocity fuel intake.
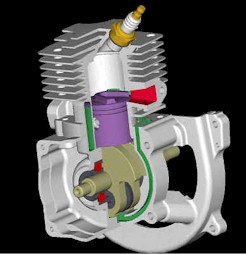 |
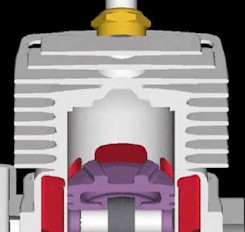 |
Image used with permission of Tanaka |
The curved surfaces come in two parts: the curved top and the U-shaped device on the
piston itself. The high velocity is created by using a smaller intake. In order for the
same amount of fuel to come in, the fuel has to come in faster. It is similar to putting
your thumb over a garden hose to make it spray water farther. As the fuel charge is
circulated through the crankcase it is prepared to maximize atomization and be placed in
"the optimum range of the spark plug for flame propagation." (R Haslam)The curved dome
contributes to more efficient fuel burning by keeping the fuel separated into
a smaller space. Thus allowing the spark plug to ignite the high quality fuel completely
and use the high quality fuel to ignite the low quality fuel, in a chain reaction that
leads to a cleaner, more complete combustion. The U-shaped component also helps herd
the fuel. The spark plug is set at an angle to the piston, so it is easier to install and
take out. With most two stroke engines, having the spark plug in the center of the top
would allow a more complete ignition. This delivery "design
is a low cost alternative to fuel injection."(R Haslam)
According to R Haslam of Tanaka, "a PureFire engine
produces the same amount of horsepower as a standard engine of similar displacement, but uses
about 30% less fuel in doing so. An uncontrolled two cycle passes as much as 30% of the fuel out the exhaust without burning
it, (cross cylinder scavenging loss). This would indicate that their efficiency is
severely impeded by their inherent, inefficient ability to utilize the fuel introduced to
the engine. Reducing the fuel intake of an engine has an obvious correlation to the amount
of emissions it generates. So in that instance, the efficiency of the engine has a
direct bearing on all emission values, including hydrocarbons, and additives in the
gasoline."
- Mechanical Logic Gates (movie)
Our engine will implement a mechanical logic-gate system to
further reduce the cross scavenging flow (raw fuel loss) and aid PureFire's exhaust port
locations/combinations.
The two plates mechanically slide
over one another and are timed by the mechanical action of the piston: plate 1 (green) is
railed to plate 2 (grey) which is attached to the piston. During the exhaust step, the
gates will slide up through a channel along the sides of the dome so that the optimal
distance between the spark plug and piston head is not compromised during the combustion
step. |
|
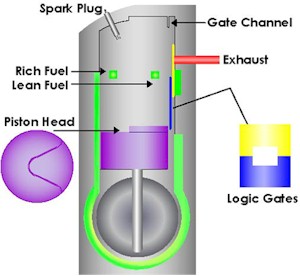
CAD.dwg file
- Activated Radical Combustion
Active Radical Combustion (ARC) is the phenomenon associated with the
common occurrence typical of two-stroke engines known as "running on"- the fact
that when electrical ignition is terminated, physical internal combustion occurs with a
pretense of spontaneity. The combustion of a hydrocarbon, most simply expressed as CxHy
+ (x + (y/4))O2 -> xCO2 + (y/2)H2O represents exclusively reactants to
products, neglecting the critical intermediates, or radicals, essential to the propagation
of ARC. The ignition of a hydrocarbon is in reality a complex multi-step process
involving a plethora of intermediaries that evolve as a result of conditions and chemicals
present in the system. This type of combustion is pivotal on the temperature of the
residual intermediate gases (radicals) and the pressure that remains in the cylinder after
the exhaust port is closed, known as Pressure at Exhaust Closing (PEC). This
pressure can easily be maintained by regulating the rate at which the exhaust escapes, and
many prototypes have been implemented in order to control the outward flow of exhaust.
Practical applications of ARC revolve around the effective utilization of
spontaneous internal combustion, unaided by devices analogous to spark-plugs. Not only
does this conserve potential power of the fuel, thus increasing efficiency, but reduces
exhaust emissions characteristic of normal two-stroke engines. For the
majority of present operations of ARC, the efficiency range that minimally compromises
environmental impact is from just above engine idle (5% throttle) to anywhere in the
vicinity of 60% throttle (comparable to 5000rpm's on a top-lining 8000rpm engine).
Anywhere above or below these parameters requires the aid of a combustion device, such as
a spark-plug. ARC occurs most optimally form 6% to 22% throttle, coincidentally
where normal two-stroke engines often experience irregular combustion and
"misfiring." Beyond 60% throttle, pollution resulting from unused fuel is
comparable to a typical two-stroke engine; therefore, the regulation of the exhaust port
during these rigorous conditions is futile.
One of the more notable applications of controlled ARC, Honda's EXP-2 off-road racer is
one of the more successful trials, where the balance between increased efficiency of clean
emissions and minimal loss of power aided in the top placement among the EXP-2's class in
both the 1995 Grenada/Daker Rally and the 1995 Baja 1000. In the EXP-2, a mechanical
valve varies the height of the cylinder's exhaust port electronically in response to
various factors including engine RPM and throttle position, thus managing pressure to
maximize efficient ARC.
In our engine, our spark plug ignition is controlled by sliding electrodes that respond
to the centrifugal force of the crankshaft. Our switch consists of a spring and sliding
rod assembly in which a portion of the contact surface is protected by a non-conductive
material (black in diagram) and will be connected to the end of the crankshaft so
that the rotation of the crankshaft will rotate the switch assembly.
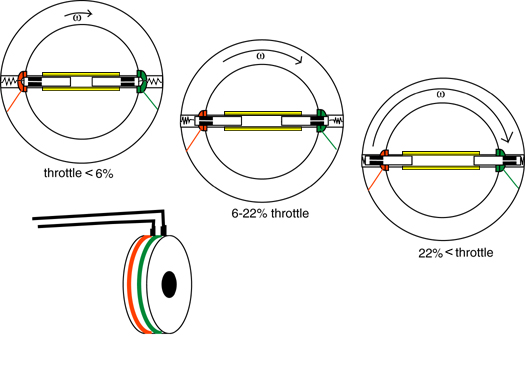
Wires leading from the dynamic switch will complete the spark plug circuit. When the
engine is at a stop, or below 6% throttle, the ends of the rod will allow current to pass
from one point to the other through the connecting yellow bar and the circuit
will be completed, allowing the spark-plug to ignite. Between 6% and 22% throttle, the centrifugal force coerces the springs to
compress as as the rods are forced outward from their central locations. During these
speeds the non-conductive material is between the electrodes and the metal rods thus
removing power from the spark-plug, allowing the engine to be powered by active radical
combustion. When the throttle exceeds 22%, the springs are compressed further allowing the
rod to slide farther outward, once again permitting electrical contact and spark-plug
ignition.
In conclusion, our engine's design incorporated three efficiency components:
- Tanaka PureFire engine's crankcase and piston dome design for fuel delivery, combustion,
and exhaust
- A mechanical logic gate exhaust system driven by the piston's motion
- A mechanical dynamic switch driven by the piston's motion that allows for two combustion
methods: spark plug and activated radicals
Each of these has a positive impact on reducing fuel emissions - either in the form of
raw fuel (cross scavenging flow) or less than complete combustion. Our purpose is to
"use less fuel while optimizing its use." (R Haslam) |
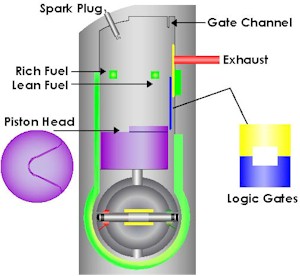 |